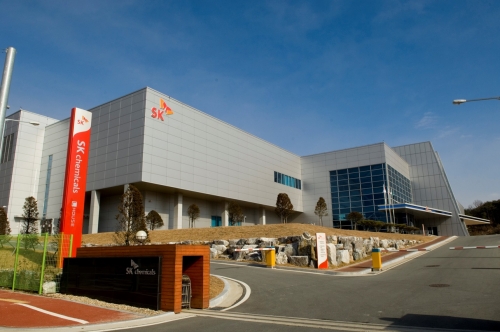
35도가 웃도는 폭염이 기승을 부린 9일 서울서 중앙고속도로를 타고 약 4시간여를 달려 경상북도 안동에 도착했다. 푸른 하늘과 어울리는 고즈넉한 분위기의 고택들이 있는 마을을 지나 약 10분을 더 달리니 최신식으로 지어진 공장 건물이 한눈에 들어왔다. 인류의 삶과 건강에 없어서는 안 될 빛의 역할을 하는 곳이 되겠다는 의미를 지닌 SK케미칼의 백신공장 ‘L하우스’였다.
L하우스는 대지면적 6만3000㎡ 규모로 2012년 지어졌다. 이홍균 L하우스 공장장은 “2009년 신종플루가 유행할 당시 우리나라는 백신이 없어 발을 굴렀다”며 “다시는 우리나라에 이런 일이 없어야 한다고 생각해 L하우스가 만들어졌고 이제는 3개월이면 백신을 공급해 생명을 구할 수 있게 됐다”고 말했다.
L하우스는 설계 단계부터 해외 진출을 목적으로 만들어졌다. 개념 설계는 영국과, 기본 설계는 미국과, 상세 설계는 한국회사와 합작해 설립됐다. 유럽과 미국 등 주요 국가의 우수한 의약품 규격을 맞출 수 있게 설계하고 건설된 공장으로 현재 △세포배양 △세균배양 △유전자재조합 △단백접합백신 등 백신 생산을 위한 선진적 기반기술 및 생산설비를 보유해 세포배양 독감 백신을 비롯한 차세대 백신을 생산할 수 있는 시설을 갖추고 있다.
또한 L하우스는 생산 과정에 사용되는 설비를 일회용 백으로 대체하는 ‘싱글유즈시스템(Single Use System)’을 적용해 제품의 안전성과 이산화탄소 배출 감소를 실천하고 있다. 그 결과 지난 2013년 미국 친환경 건축물 인증제도인 ‘LEED(Leadership in Energy and Environmental Design)’에서 제약 공장 중 세계 최초로 골드 등급을 획득했다.
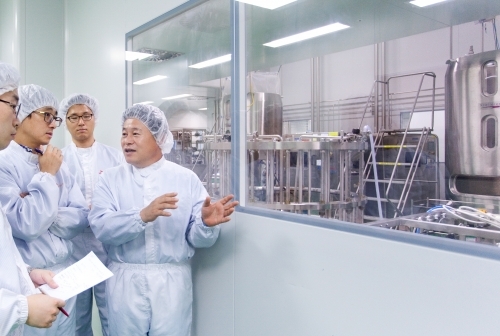
▲ 들어가는 절차부터 까다로운 L하우스
백신공장인 만큼 다른 현장 방문과정과는 들어가는 절차부터 달랐다. 외부에서 먼지나 세균이 들어오는 것을 막고자 손세척과 손소독은 물론 플랜트 유니폼(파란색 유니폼) 과 무진복(하얀색 유니폼)을 겹쳐서 껴입고 신발덮개, 헤어캡을 두 개씩 착용하고 나서야 안에 출입할 수 있었다.
L하우스의 내부는 마이크로 먼지 수에 따라 A, B, C, D, CNC, NC 등급으로 나눠진다. CNC는 ‘Controlled Not Classfied’로서 관리구역이나 분류는 하지 않는 구역을 일컫고, NC는 ‘Not Controlled’ 로 두 곳은 플랜트 유니폼만 입고 들어갈 수 있다. 그러나 D단계부터는 무진복까지 입고 들어가야 출입할 수 있다. B단계인 프리필드시린지 충전실의 경우 무균지역으로 눈코입을 모두 가린 무진복을 입고 들어가야 하며 최고 단계인 A단계는 사람은 출입할 수 없고 장갑을 낀 손만 들어갈 수 있다.
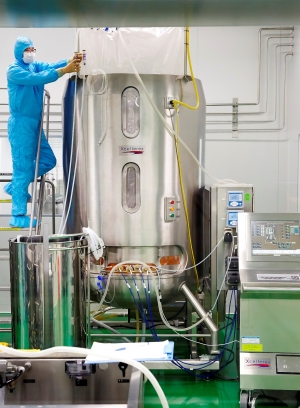
▲ SK케미칼 백신의 핵심 기술 최첨단 무균 배양기 ‘바이오리액터’
L하우스의 1층 생산공장은 원액 생산실과 충전ㆍ포장을 하는 완제 생산실로 나뉜다. 원액 생산실에는 일회용 무균백을 활용해 2000ℓ의 세포 원액을 배양할 수 있는 무균배양기 바이오리액터가 있다. 이곳에서는 세포 배양이 이뤄지기 때문에 출입 절차가 더 까다로웠다. 무균복으로 한 차례 옷을 더 껴입고 들어가야 하며, 두 개의 문 위에는 바깥공기와 안쪽 공기를 차단하는 에어록이 존재했다. 바깥공기가 내부로 들어오면 빨간 불이 들어오며 ‘삑삑’ 소리가 났다.
또한 내부에서는 천장 위에 팬이 내부에 공기를 공급하고 바닥의 팬이 외부 공기를 밑으로 배출시켜 깨끗한 공기가 순환되게끔 유지되고 있었다.
SK케미칼의 세포배양 독감백신은 동물세포 배양액을 이용해 백신을 생산한다. 공장 내부에 자리 잡은 커다란 스테인리스통(바이오리액터)에 담겨 점차 부피를 늘리는 방식으로 배양된다. 2대의 스테인리스통은 일회용 무균백으로 쌓여 있었다. 공장 관계자는 “무균백의 한 장당 가격은 약 1000만 원”이라며 “보통 다른 업체들은 무균백을 쓰지 않고 주사용수로 세척해 사용하지만 SK케미칼은 무균백을 사용한 후 멸균 후 폐기해 제품의 안전성과 이산화탄소 배출 감소를 실천하고 있다”고 설명했다.
2000ℓ 바이오리액터에서 배양된 세포들은 1ㆍ2차 정제를 거쳐 최종 여과된 후 백신으로 탄생돼 완제 생산실로 옮겨지게 된다.
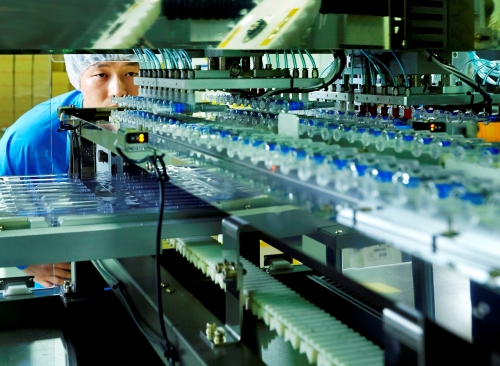
▲ 프리필드시린지, 바이알(동결건조), 경구용 백신 등 다양한 제형으로 탄생
완제 생산실은 원액 생산실보다 단계가 낮아 플랜트 유니폼을 입고 들어갈 수 있었다. 가장 먼저 눈에 띈 것은 통유리로 구성된 충전실이었다. 이곳은 무균지역으로 두 명의 사람이 얼굴까지 가린 하얀색 무진복을 입고 프리필드시린지(주사기) 충전기계의 오류가 없는지 확인하고 있었다.
이홍균 공장장은 “사람의 표피에서도 바이러스가 있을 수 있기 때문에 얼굴까지 모두 가린 복장을 입은 것”이라며 “충전실 기계 안은 A 등급으로 장갑으로만 만질 수 있다”고 설명했다.
충전해서 나온 프리필드시린지와 바이알(유리병) 등은 이물질 검사와 정품 검사를 거쳐 라벨링을 붙인 뒤 블리스터 포장기를 거쳐 포장하는 사람들에게 전달하게 된다. 이들은 마지막까지 불량품을 검수한 뒤 설명지와 함께 박스에 백신을 넣고 포장한다. 이렇게 세상에 나온 다양한 제형의 백신은 국내뿐 아니라 해외로 수출된다.
SK케미칼은 지난 2008년부터 백신 사업 인프라 구축과 R&D에 약 4000억 원을 투자해왔다. 그 결과 지난해 성인용으로는 국내 최초, 소아용으로는 세계 최초로 세포배양 3가 독감백신인 ‘스카이셀플루’를 출시해 첫해 주문·판매량 360만 도즈를 돌파했으며, 올해는 스카이셀플루4가 500만 도즈를 생산해 이달 중 전국 병의원에 유통될 예정이다.
이홍균 공장장은 “스카이셀플루4가의 국내 판매 시작되면 생산량을 늘릴 것”이라며 “현재 자체 생산한 제품의 수출뿐만 아니라 다른 회사 제품을 생산한다거나 공장 건설을 하는 등 다양한 방식으로 해외 진출을 진행하고 있다”고 밝혔다.