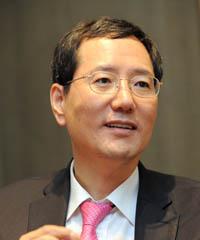
4차 산업혁명에서 제조 혁신의 핵심은 데이터와 인공지능을 활용한 현실과 가상의 융합이다. 기존의 제조업에서 불가능했던 최적의 제품 생산과 고객 관계의 융합화를 통해 제조업은 새롭게 탄생하고 있다. 구체적으로 아디다스의 스피드 팩토리의 사례를 보자. 아디다스가 중국, 베트남 등지의 생산 거점을 떠나 독일의 안스바흐에 새로운 신발 공장을 건설한 것을, 흔히들 제조업의 귀환인 리쇼어링(Re-shoring)이라고 일컫는다.
그러나 스피드 팩토리의 진정한 의미는 리쇼어링이 아니고 E2E(end-to-end)의 생산과 소비의 융합으로 보아야 한다. 안스바흐 공장의 총 인원은 160명 수준이고 생산 현장은 10명 내외가 근무하고 있다. 즉 고용창출 효과가 크지 않다는 점에서 리쇼어링의 의미는 퇴색한다.
현재 ‘대량 생산’의 신발산업 구조는 다음과 같다. 다음에 유행할 신발 디자인을 선정하고 필요한 원·부자재를 대량 발주하고 이를 아시아의 저임금 국가로 운송한 후 일관 생산을 하고 소비 국가로 선적해 대규모 창고에 대량 재고를 두고 도·소매점을 통해 판매하는 구조다. 이 과정은 대체로 18개월이 소요된다. 18개월 이후 유행할 디자인 선택과 대량 재고와 판매 부진은 기업의 리스크다. 이러한 생산과 소비의 괴리 현상을 4차 산업혁명 기술로 극복하자는 도전이 스피드 팩토리가 갖는 진정한 의미인 것이다.
소비자는 스마트폰으로 디자인과 색깔을 고르고 아라미스라는 모션 캡처 기술로 맞춤 신발을 주문하면 24시간 내에 배송받는다는 것이 가장 큰 혁신이다. 개별 고객과 거대 기업이 ‘대량 맞춤’의 E2E의 융합을 하게 된 것이다. 주문 후 5시간 내에 카본3D의 초고속 3D프린터가 150개에 달하는 신발 자재를 개별적으로 인쇄하고 로봇이 이를 자동으로 조립한다. 실시간 생산 이후 O2O배송 업체를 활용해 24시간 내에 주문에서 배송까지 완료된다. 과거 5주 이상 걸리던 맞춤 생산과 비교해 보라.
스피드 팩토리는 아디다스와 독일 정부, 아헨공대가 3년 이상 심혈을 기울인 합작품이다. 스마트 공장은 지멘스의 마인드 스피어에 기반을 두고 있다. 각종 센서와 시스템 등은 20 개 이상의 기업들이 참여해 구축했다. 안스바흐의 스피드 팩토리는 지멘스의 암베르크 공장에 이어 독일 제조혁명의 테스트베드라고 할 수 있다.
대량 생산에서 대량 맞춤으로 전환되면서 고객과 기업은 융합된다. 스피드 팩토리의 진정한 의미는 온 디맨드(On-demand)와 온 서플라이(On-supply)의 결합이고 제조와 서비스의 융합이다. 그러나 아직도 가야 할 길은 멀다. 안스바흐 공장의 50만 켤레 생산량은 아디다스 전체 생산량인 3억6000만 켤레의 0.2%에도 못 미친다. 뿐만 아니라 신발끈 공정 등은 아직도 인간에 의존하고 있는 실정이다.
그래도 시작이 절반이다. 스피드 팩토리는 지속적으로 진화할 것이고 전 세계로 확산할 것이다. 그리고 제조업의 대량 생산 개념은 이제 맞춤 생산 개념으로 전환될 것이다. 이제 대한민국의 제조업이 추진해야 할 혁신의 방향을 다음과 같이 제시하고자 한다.
첫째, 클라우드 기반 스마트 공장의 확산을 가속화하고, 클라우드 바우처 등으로 스마트 생산의 공유경제를 촉발하라. 둘째, 데이터 기반 제조-서비스 융합인 DPSS(Data Product Service System) 개념에 입각해 고객과 융합하는 제조업의 가치창출을 촉구하며 이를 스마트 공장 프로젝트에 포함하라. 셋째, GE의 프리딕스와 지멘스의 마인드스피어에 견줄 산업 인터넷 컨소시엄을 전 산업적으로 구성해 글로벌 경쟁력이 있는 산업 플랫폼을 구축하라.