EF쏘나타 ‘B보디’로 옵티마 개발
엔진ㆍ변속기 공유하며 비용 감축
디지털 디자인 도입해 개발 기간↓
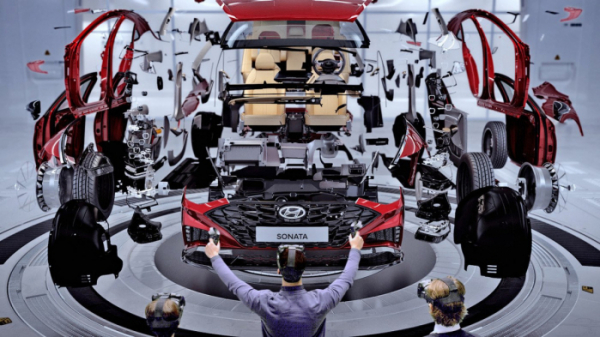
지난 5년간 3000억 원의 연구개발비를 투입한 우리 차는…
1990년대. 신차발표회에 등장한 자동차 회사의 임원들은 ‘우리가 이만큼 큰돈을 들여 신차를 개발했다’는 것을 강조했다. 이른바 단골 멘트였던 셈이다.
당시 자동차 업계는 “이대로 머물러서는 안 된다”라는 절박함에 빠졌었다. 일본(미쓰비시ㆍ마쓰다)과 미국(GM), 독일(오펠)의 완성차를 가져와 생산을 대행하는 일이 많았다. 주문을 받아 생산을 대신했고 이들 대부분을 수출했다. 이 가운데 일부가 한국 시장에 팔리는 구조였다.
현대차가 일찌감치 포니를 앞세워 고유모델 개발에 나섰지만, 나머지 브랜드를 그러지 못했다. 결국, 우리 손으로 만든 우리 차가 절실했고, 그렇게 자체 기술을 앞세워 고유 모델 개발에 나서기 시작했다.
사정이 이렇다 보니 막대한 연구개발비용이 필수였다.
개발비용을 아끼기 위해 다양한 방법을 활용하기도 했다. 기아는 일본을 비롯해 글로벌 주요 제조사의 부품을 ‘카피’하는데 선수였다. 설계도를 주지 않으면 해당 부품을 하나하나 분해하면서 설계도를 그렸다. 이른바 ‘역(逆)설계’였다. 덕분에 당시 기아 연구개발진을 일컬어 ‘세계 최고 수준의 역설계 집단’이라는 찬사 아닌 찬사가 이어지기도 했다.
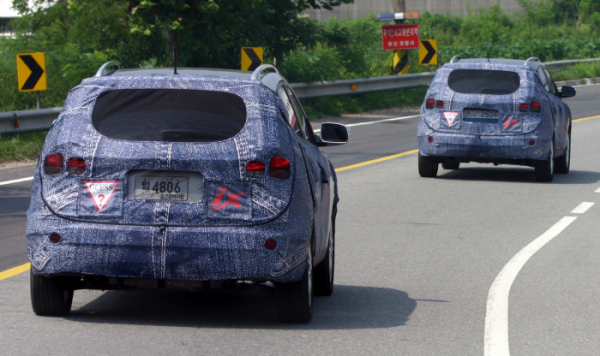
2000년대 들어 “0년 동안 0000억 원을 투입해 신차를 개발했다”는 멘트는 사라졌다. 왜일까?
본격적으로 다품종 시대를 맞이하면서 자동차 회사의 여러 차종이 핵심부품과 플랫폼을 공유하기 시작했다.
잘 만든 엔진 하나를 여러 차종에 두루 얹기 시작한 것. 변속기는 물론 언더보디의 서스펜션, 주요 부품과 내장재ㆍ심지어 시트 프레임까지 공유했다. 개발비를 줄이는 한편, 더 많은 부품을 주문해 부품단가를 낮추겠다는 전략이었다.
이후부터 자동차 연구개발비는 감소하기 시작했다. 수많은 대중 앞에서 “수천억 원을 들여 개발했다”고 자랑하기 어려운 시대가 도래한 셈이다.
요즘은 자동차 개발에 로봇이 도입됐고, 컴퓨터가 도면을 그린다. 정밀한 장비가 한 치의 오차 없이 각종 부품도 설계한다. 심지어 설계와 디자인 과정에서 부품의 가격까지 도출할 수 있다.
제조사마다 단계가 다르지만 통상 ①선행 개발 ②상품 기획 ③제품 계획 ④설계 ⑤양산 설계 등을 거친다.
선행개발은 이 차를 개발해야 하는 이유가 무엇인지, 어떤 시장에 어떤 고객층을 대상으로 차를 개발하는지 결정한다. 상품기획의 전 단계인데 상대적으로 추상적이다.
다음 단계는 제품기획이다. 시장에서 어떤 차와 경쟁할지를 결정한다. 이 단계를 전후해 자동차의 디자인도 결정한다. 보다 구체적으로 차의 겉모습이 드러나는 단계다. 동시에 새 모델로 얻을 수 있는 수익구조, 출시 시점, 출시 시점의 환율과 국제유가, 출시 시점의 법적 또는 제도적 규제 등을 미리 파악한다.
이 단계에서 디자인을 결정한다. 자동차 디자인도 예전보다 더 정교하고 빠르게 진행할 수 있다. 이른바 ‘디지털 디자인’을 도입한 덕이다. 디자인을 이 정도로 바꾸면 공장의 생산설비를 얼마만큼 교체해야 하는지도 결정할 수 있다.
대표적인 사례가 기아 쏘울이다. 1세대에서 2세대로 거듭나는 과정에서 디지털 디자인을 도입했다. 개발비용과 공장설비 교체를 최소한으로 묶어둔 상태에서 디자인 변경 범위를 도출한다. 그리고 그 범위 안에서 차의 겉모습을 변경해 디자인했다.
사정이 이렇다 보니 신차 개발 주기가 크게 단축됐다. 7년마다 내놓던 ‘풀모델 체인지’를 5년, 짧게는 4년마다 내놓을 수 있게 됐다. 시장 트렌드 변화에 명민하게 대응하는 한편, 수요와 고객 요구사항을 발 빠르게 신차에 반영할 수 있게 됐다.
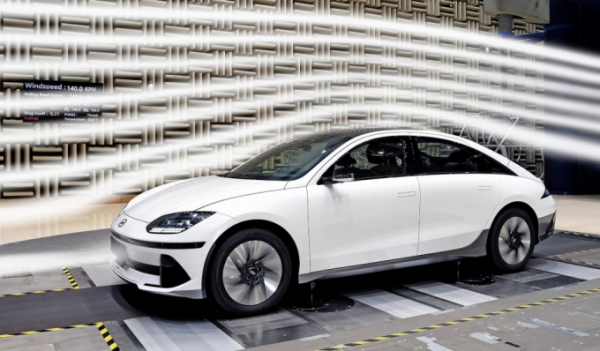
정답부터 말하자면 산정이 불가능하다. 산정이 됐다 해도 제조사에서 손꼽는 영업기밀이다. 기준을 어디에 맞추느냐에 따라 천문학적인 금액이 될 수도 있고, 별다른 투자 없이 뚝딱 차를 내놓을 수도 있기 때문이다.
2000년에 등장한 기아 옵티마의 경우 현대차 EF쏘나타를 개발하는 과정에서 막바지에 탈락한 디자인을 가져왔다. 엔진과 변속기는 물론 내장재 대부분을 공유했다. 그렇다고 기아 옵티마의 연구개발비용에 EF쏘나타의 개발비를 포함할 수 없다. 요즘 차들이 이런 구조다.
개발 막바지에는 P1과 P2 단계를 거쳐 이른바 ‘PP(Pre Product)카’가 등장한다. 사전 양산차다. 본격 생산에 돌입하기 전에 양산한다는 가정하에 일정량의 시험차량을 생산하고, 양산 전까지 실차 테스트를 시작한다. 이 단계에서 부품사들에 시험차를 제공하고 내구 테스트를 맡기는 데 이 단계에서 디자인이 많이 유출된다. 전 세계 곳곳을 누비며 내구성을 테스트할 때 들어가는 비용도 연구개발비다.
이런 개발 과정은 제조사마다 다르다. 세부 내용도 엄중한 보안이다.
결국, 이전보다 차 개발비용이 유사하게 투입되면서도 더 많은 기술을 담을 수 있는 시대가 됐다. 여기에 개발 기간도 단축됐다. 이미 보유 중인 신기술을 가져오면서 비용과 시간이 줄어든 셈이다.
그렇다고 마냥 “값싸게 차를 개발했다”라며 제조사를 폄훼할 수는 없다. 값싸게 차를 개발하는 것도 제조사의 기술력이자 능력이기 때문이다.
따라서 차 개발에 얼마가 투입됐느냐는 더는 유의미한 명제가 아니다.
다만 종이 한 장에 머물러 있던 자동차 한 대가 우리 눈앞에 등장할 때까지 밤잠을 줄여가며 열정을 불태운 수백 수천 명 연구원의 노력은 돈으로 환산할 수 없는 한국차의 가치라는 사실을 잊지 말아야 한다.