
“LG전자 평택 공장은 칠러 개발과 생산에서 세계 최고 수준의 인프라를 갖췄다고 자부합니다.”(박영수 LG전자 칠러BD담당 상무)
28일 경기도 평택에 있는 LG전자 칠러 사업장에 들어서니 14만8000㎡ 대지에 세워진 베이지 톤의 건물들이 마치 세련된 조선소를 연상케했다. LG전자는 지난해 11월 칠러 사업 규모를 확대하고 연구개발을 강화하고자 2000억 원을 투자해 전북 전주에 있던 칠러 공장을 평택으로 옮겼다.
박영수 상무는 “평택디지털단지에 산업연관성이 높은 생산기술원이 있어 시너지를 낼 수 있고, 인근에 평택항이 위치해있어 수출 물량을 항구까지 운송하는 데도 강점이 있다”고 이전 이유를 설명했다.
평택 공장은 제품을 만드는 생산동 6기와 연구개발을 하는 연구시험동 4기로 이뤄졌다. 평택공장의 연간 최대 생산량은 냉동기 기준 1000대 수준이며, 냉동기에 연결되는 실내기 등 부속 제품을 포함하면 2000대까지 늘어난다.
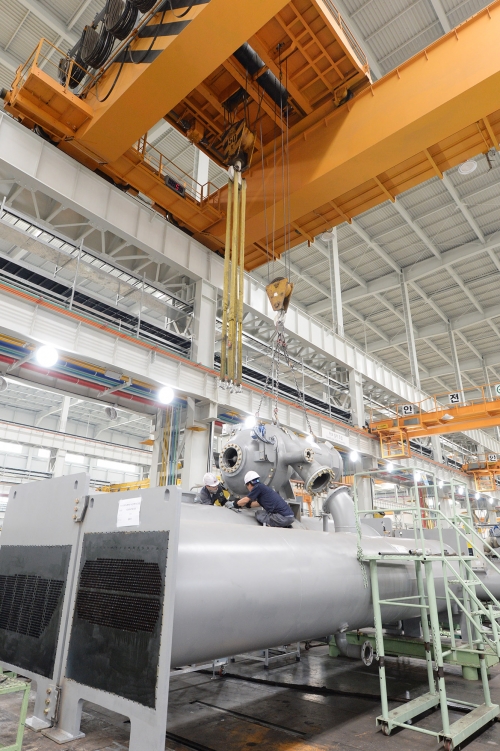
칠러를 설계하고 제작하는 생산동에 들어서자 가장 먼저 천장에 있는 크레인이 눈에 띄었다. 총 11대의 오버헤드 크레인과 벽에 세워진 젠트리 크레인 20대는 최소 20kg에서 최대 50톤에 이르는 부품과 완제품을 이동하는 역할을 한다.
차가운 바람을 만드는 칠러를 제작하기 위해 더운 날씨에 직원들은 뜨거운 구슬땀을 흘리고 있었다. 직원들은 자신의 키보다 두 세배 높은 칠러에 올라가 조립과 용접, 테스트작업을 하고 있었다.
먼저 철판 원통에 사람이 들어가 용접작업을 통해 찬물을 만드는 열교환기를 만들고, 2~3명의 작업자들이 짝을 지어 부품을 조립한다. 윤활유를 대신해 냉매 가스가 윤활작용을 하는 LG전자의 무급유 터보 칠러는 기능물을 뿌려 냉매가 세지 않는 지 1차 누설 검사를 한 후 △진공 누설 △헬륨 누설 △수압 압력 검사 등을 진행한다.
고명해 칠러생산팀장 부장은 “산업설비에 설치하는 터보칠러를 만드는 공정은 까다롭고 보안유지가 철저하다”며 “초미세 누설량까지 측정해 연간 30cc 미만의 누설이 될 경우 정상처리한다”고 말했다.
이후 성능시험 설비를 거쳐 최종적으로 이상이 없는 지 확인한 후 9M 높이의 대형 콘테이너인 도장 부스에 들어가 색을 입히면 최종적으로 칠러가 탄생된다. 고 부장은 “각국마다 전압과 주파수가 달라 성능시험 설비에서 200V~1400V까지 전압과 50Hz, 60Hz의 주파수를 공급해 철저하게 테스트 하고 있다”며 “도장 부스도 품질을 고르게 하기위해 적정 건조 온도인 60도로 유지해주는 자동화 건조설비를 작용했다”고 설명했다.
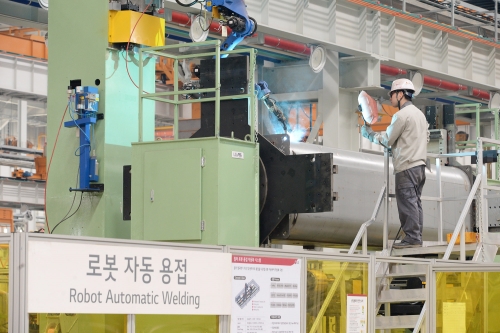
또 생산동에서 눈에 띄는 것은 로봇 자동 용접이었다. 칠러는 100% 주문제작 방식이기 때문에 제품에 따라 용접위치가 달라 공정 자동화가 쉽지 않다. 그러나 LG전자는 세밀한 용접 작업과 작업자의 근무여건 개선을 위해 국내 최초로 3월 용접 로봇을 생산현장에 도입했다. 용접 로봇을 통해 오차율 ‘0(Zero)’의 세계 최고 수준의 용접 품질을 구현하고 있다.
생산동 옆에는 연구시험동이 자리잡고 있었다. 칠러의 핵심 신기술과 시제품을 테스트하는 곳으로 평택공장을 지으면서 전용 공간을 따로 만들어 가장 집중 투자했다. 이남수 칠러선행연구팀 수석연구원은 “초창기와 비교해 현재 LG전자의 칠러 기술력은 글로벌 톱티어들과 견주어도 차이가 없다”며 “연구시험동은 세계 최고 수준이라 자부할 수 있으며 LG전자는 앞으로 이곳을 통해 칠러 기술 확보에 집중할 것”이라고 말했다.